You write:
“CITS has two patent applications it seems. One each for the flap and by-pass valve.
Previous crosshead marine engines have wet sump covered I guess so no patents there. CITS as I see it is a variation on a theme and only the valve patents prevent anyone productionising it if they wanted to. Skip his valves and go straight to crosshead and wet sump - if you want. Are his valves really that much better than simple reeds? Does his increase in crankcase compression from 1.4-1.5:1 to 1.6:1 really incur throttling losses that justify or need a by-pass valve?”
The core idea behind the CITS seems to be the reduction of the pumping loss when a 2-stroke operates at lower revs / light loads (i.e. wherein the 2-strokes suffer).
CITS tries to bring to the 2-stroke engines what the Attkinson / Miller cycle brings to the 4-stroke engines (many of the modern fuel-efficient 4-strokes use, in a significant degree, the Miller cycle; for the basic Miller patent click on http://www.pattakon.com/tempman/Miller_patent.pdf )
At light loads the pumping loss is a significant part of the indicated power.
With the PatAir of pattakon (more at http://www.pattakon.com/pattakonHydro.htm ) the 4-stroke avoids the sub-pressure during the induction, and so it reduces the relative pumping loss (an advantage that comes together with other advantages like the lower temperature of the cycle etc).
The PatAir of pattakon is actually a slight modification of the MultiAir / TwinAir system of FIAT - Chryshler / INA – Schaeffler.
The modification is slight, however the difference it brings is big / significant because it offers an infinity of additional more-fuel-efficient modes to the modes already available with the MultiAir / TwinAir of FIAT :
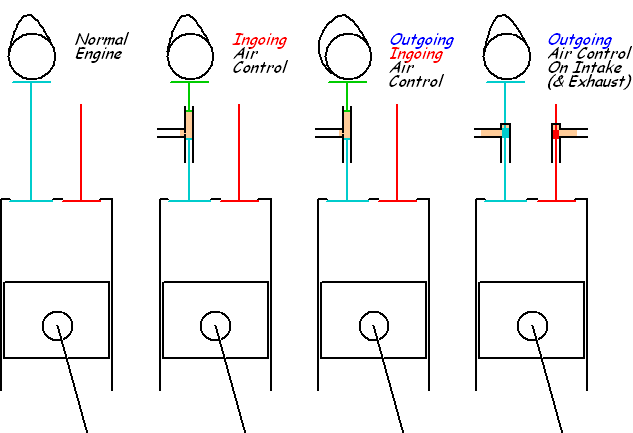
The following plot helps to get the difference:
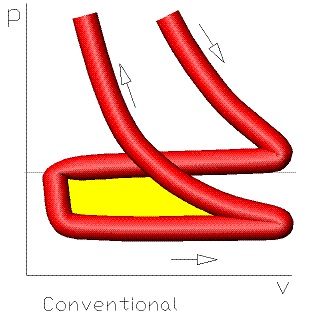
In the PatTwo patent (post in page #113 and page #116) it is explained where the CITS engine of Basil Van Rooyen fails to do what it is supposed it should do.
The variation of the total volume of the two cooperating spaces under the two pistons of the CITS engine spoils the operation of the engine at lower revs / light loads, i.e. exactly where it is supposed it brings the best improvement.
As noted in U.S. Pat. No. 8,683,964 of Basil Van Rooyen (CITS):
"In practice a butterfly valve maybe provided in the inlet conduit, not for throttle control but for the purpose of idle setting. Above these very slow idle speeds, this butterfly valve would open fully, and the engine speed and power would be controlled solely by the by-pass valve, and not by the butterfly valve or any other throttle arrangement upstream of the bifurcation point.”.
The PatTwo design does not need such a throttle valve because the sum of the volumes of the two cooperating spaces is constant (either in the single combustion chamber / conventional version, or in the double acting piston / harmonic version; more at http://www.pattakon.com/pattakonPatTwo.htm ) .
The difference gets clearer if you think the case a PatTwo engine:
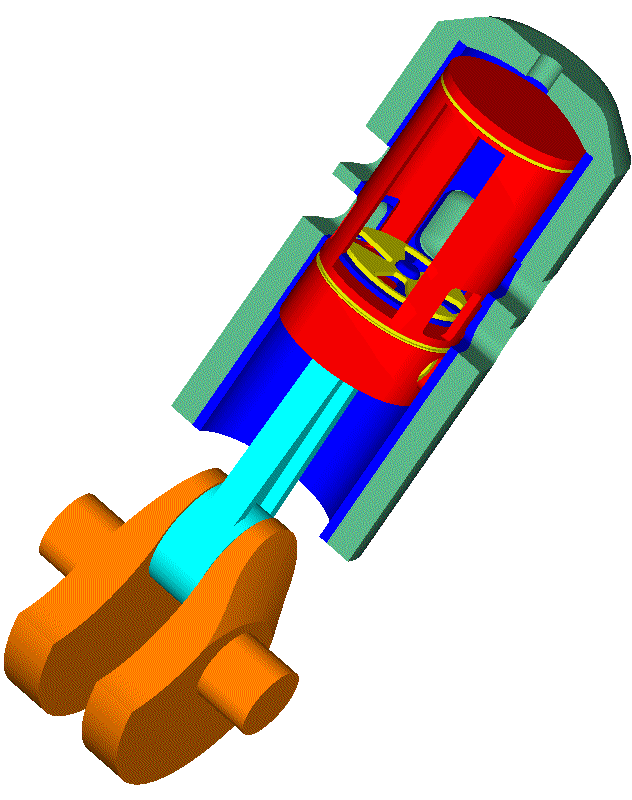
is running at idling (or at light load / low revs), with the passageway between the two spaces, above and below the “separator” (inside the piston), communicating freely.
Isn’t it the Miller cycle applied in a 2-stroke?
(What happens in a 4-stroke “unlimited” (as the PatAir) Miller at idling / light loads? The fresh air or mixture enters into the cylinder through the intake valves and then (as the piston performs its “compression stroke”) most of the air or mixture entered in the cylinder returns back to the intake manifold though the still open intake valves (LIVC), without creating significant subpressure or pumping losses).
The PatTwo is good not only for light loads / lower revs.
At higher revs / heavier loads the PatTwo design offers new opportunities, like the “variable” crankcase “dead volume": depending on how much open or close is the throttle (or control) valve, the crankcase behaves as having from quite small to quite large dead volume. With a tuned exhaust . . .
Thanks
Manolis Pattakos