McLaren MP4-1
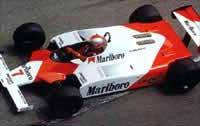
Active: 1981
Team: McLaren International Ltd
Designer: John Barnard (CD)Drivers: John Watson (7), Andrea De Cesaris (8 )
McLaren rocked Formula 1 with its first composite design. Twenty five years on, it is still leading the way
March 6, 1981, was a day that changed the motorsport world. When McLaren unveiled its carbon-composite MP4-1 chassis to an expectant press corps at a rain-swept Silverstone, it wasn't only the journalists who felt the breeze. The winds of change blew through the entire sport.
The MP4-1 was the first fully composite Formula 1 chassis, designed as a moulding, rather than the traditional series of flat aluminium panels mechanically fixed together. The design team had challenged conventional thinking on both the materials used and the method of construction. Their reward was a gigantic leap in strength and stiffness that would revolutionise racing car design.
Pioneering new frontiers of composite technology has subsequently become a hallmark of the McLaren Group. The record-breaking McLaren F1 became the world's first fully composite production road car. The follow-up project, the Mercedes-Benz SLR McLaren, represented an even bigger achievement: bringing composite technology to the mass market. Engineers had to rip up the rules and invent new technology to produce the first-ever series production sports car to feature entirely carbon-composite bodywork and a monocoque chassis.
In racing, Team McLaren Mercedes is continuing to break new ground. Its latest Formula 1 challenger, the MP4-21, is the most advanced composite Formula 1 design the team has ever produced. "There is a night-and-day difference between the MP4-1 and the MP4-21 but, although the techniques and materials have changed, the core principle remains the same," reveals Neil Oatley, Design and Development Director, McLaren Racing. "In 1981, very few structural components were made in composites, so it was a huge leap forward in motor racing technology to commit to a chassis in that material. John Barnard, head of the MP4-1 design team, was an adventurous engineer who wanted to push the boundaries." And push he did. As many as 50 sections of aluminium were required to produce a conventional monocoque, but the MP4-1 was constructed from just five major composite mouldings. The strength of the carbon fibre relied on loads being fed along the axis of the strands, giving the structure a much higher stiffness-to-weight ratio than aluminium. This breakthrough would revolutionise Formula 1 safety, but the technology was initially treated with suspicion. -Race car designers were traditionally mechanical engineers with little experience of dealing with these materials," recalls Oatley.
Yet once rivals grasped the benefits McLaren had harnessed, every team on the grid quickly followed its lead. Today, over 60 per cent of the Team McLaren Mercedes Formula 1 car is constructed from carbon fibre. The use of composite technology has been extended to include all of the suspension parts, and the team also boasts the only race-winning carbon fibre composite gearbox casing. "To have used this technology in such hostile environments, where components are subject to extreme loads, temperatures and vibration, would once have been a huge step in the dark," says Oatley. -But our knowledge has increased to the point where these developments are now safe and considerably worthwhile."
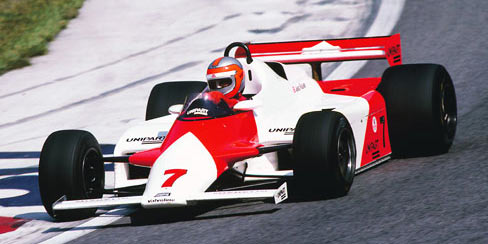
The drive to improve both safety and performance has been a catalyst for the development of new materials for the MP4-21. Cutting-edge techniques such as resin infusion, which was perfected on the Mercedes-Benz SLR McLaren, have also been introduced for some components. Work on the new car's composite structures started last summer with Finite Element Analysis (FEA) of the MP4-20, to determine how its complex mix of fibres and resin could be improved.
"That analysis enabled us to build on the good stiffness-to weight ratio, crashworthiness and compact size of the MP4-20," says Steve Foster, Senior Design Engineer - Composites. "The FIA is looking to significantly increase the pass criteria for its crash tests over the next few years, and we have gone in a slightly different direction to better meet those requirements." In some instances, the results have been spectacular. "We have improved one of the crash structure's ability to absorb impact energy significantly, without increasing its weight," Foster reveals.
Great strides have also been made with manufacturing techniques. Featuring hundreds of layers of plies, each individually tailored for stiffness or strength, the construction of a Formula 1 chassis is complex, involving more than 2000 man-hours of labour. A computer templating system has improved accuracy and quickened the process. "We now use laser technology to position the individual plies, rather than cutting out cardboard templates and using rulers to measure where each sheet of laminate is positioned," says Foster. "Much of that work can now be achieved at the press of a button, and the lasers reduce the margin of error and save time."
While the MP4-1 was designed in conjunction with a US aerospace company, McLaren Racing now has an in-house composites facility. More than 80 people work in the department, which features six autoclaves in which materials are cured. The facility enables the manufacture of composites around the clock, more than halving the original time from design to finished product. The relationship with the Advanced Composites Group, an Official Supplier of materials to Team McLaren Mercedes, is also an important asset. ACG are continuously developing their products and currently supply between 40-50 grades of advanced composite to McLaren. "They are very accommodating in terms of the demanding timescales that Formula 1 imposes on them," says Foster. -Their laboratories and chemists also offer excellent technical support."
But the biggest testament to the McLaren Group's progress is that where composite development was originally driven by the space race, the wheel has now turned full circle. McLaren has developed composites for a number of space projects, and its work has been commended by NASA. Praise doesn't come any higher.
The Driver's Verdict
"Like flying in Concorde when you've only ever flown in a 707," is John Watson's assessment of the MP4-1, the car in which he delivered the first win of McLaren's modern era. His landmark victory at Silverstone in the 1981 British Grand Prix was the highlight of a season that he had entered with a mix of excitement and trepidation.
"A composite carbon fibre chassis was a big step into the unknown," he says. "The question all Formula 1 drivers were asking was what was going to happen in an accident?" The Ulsterman found out early in the test programme that the unyielding nature of the carbon fibre was very different to the steel and aluminium panels he was used to. "My first major discovery was that if you banged your elbow in the cockpit, there was no give at all - it really hurt!" he recalls. Team-mate Andrea de Cesaris demonstrated the car's structural integrity by walking away from a number of crashes. Watson found out for himself when he escaped from a 140mph crash that destroyed the car at Monza 's daunting Lesmo bends. "Fortunately, the design turned out to be virtually bulletproof," he says. "It's easy to take a new material and apply old thinking, and many people didn't understand the technology at first. But John Barnard and his team weren't into gambles - they knew exactly what the materials would give them. The MP4-1 was born out of incredible vision."
A version of this article originally appeared in the February 2006 edition of Racing Line, the McLaren Group's in-house magazine.
Source: Racing line magazine