In the following “drawing”:
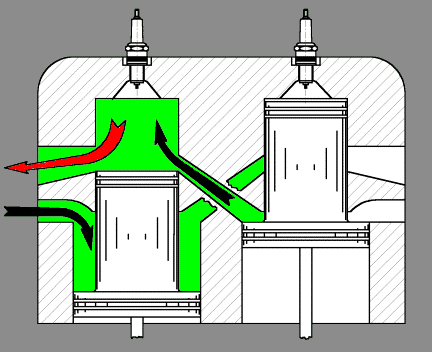
(from the http://www.bernardhooperengineering.co.uk web site of Bernard Hooper, “former Chief Engineer of Norton Villiers, responsible for the highly successful Norton Commando”),
the skirt of the “compressor” piston appears more than short.
Looking for a good photo or drawing of Hooper’s step piston in his web site, nothing was found (!).
Searching in the US-PTO (at http://patft.uspto.gov/ ) for patents granted to Bernard Hooper, here is the first page of his first / basic patent:

and here is the fifth figure (at left) with the addition of the 1st claim (at right) in the same page:
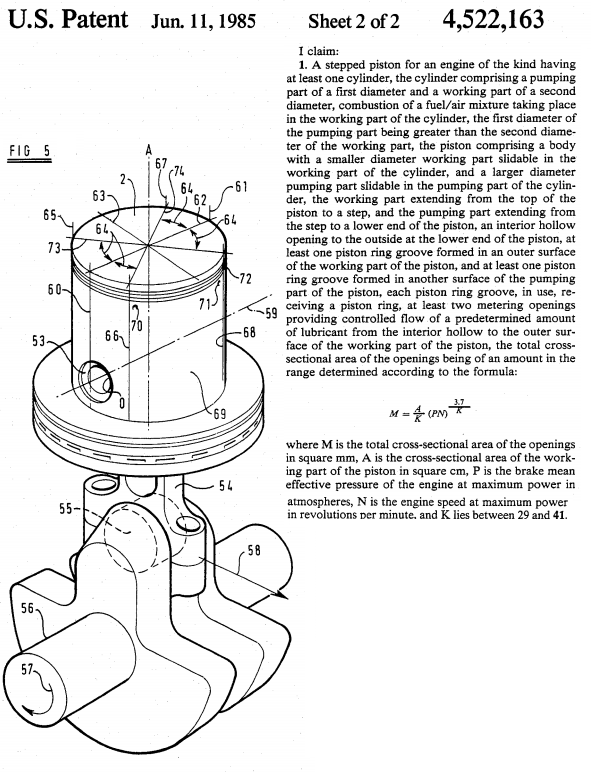
Reasonably the wrist pin should be located underside the lower ring (the oil scraper ring) of the big diameter part of the step piston.
In order to have a “over-scavenging” of, say, 25%, the diameter of the compression end of the step piston of Hooper needs to be 1.5 times ((1,5^2) –1 = 1.25) the diameter of combustion end of the step piston: the combustion piston occupies a big part of the area of the compression piston.
These two photos (they are from the proposed power-point presentation for the Engine Expos of 2008 and 2009 at Stuttgart Germany, it is available at http://www.pattakon.com/opre1_files/pattakonOPRE.pps ) :


show a different kind of step piston.
The diameter of the combustion end is 80mm, while the diameter at the compressor end (the end at the wrist pin side) is 90mm.
And because (90/80)^2=1.265
The “geometrical” “overscavenging” ratio is 26.5%.
For the same combustion piston diameter (80mm) and the same “over-scavenging”, the piston rings at the compressor end of Hooper’s step-piston would be 120mm instead of the only 90mm used in the OPRE pistons.
Differently speaking, with 120mm “compression piston diameter”, the “over-scavenging” in the above OPRE would be: 125% (not 25%, as in Hooper’s engine, but 125%).
Bernard Hooper mentions, in his web site, a 200:1 fuel/oil ratio used in his prototype step-piston engines (against the typical 50:1 of the conventional 2-strokes of that era).
As the Achates with the side crankshafts, similarly the Step Piston architecture can reduce substantially the lubricant consumption of the 2-strokes.
The one (Achates Power) eliminates the thrust loads, the other takes the thrust loads away from the cylinder liner whereon the ports are.
In the link of Tommy Cookers
(i..e. the presentation at Engine Expo 2014, Stuttgart Germany, of the step piston technology by:
Dr Peter Hooper (son of Bernard Hooper?)
BEng (Hons), PhD, CEng, FIMechE, PgCert, FHEA
Senior Lecturer in Mechanical Engineering
School of Engineering, Auckland University of Technology,
City Campus, WS Building, St Paul Street, Auckland, New Zealand)
the big part (more than half of the slides) of the presentation deals with the reduced “torque fluctuation” of their multicylinder V-4 (and others) arrangement, which leads to better NVH properties and so to better Range Extender Modules (REM) for electric cars.
An OPRE having secured on each of its two crankshafts an electric generator solves the “torque fluctuation problem” in a different and absolute way: it cancels out, internally, any free inertia and combustion torque, leaving the basis of the OPRE REM (or the basis- i.e. whereon it is mounted, of the OPRE electric generator set) perfectly rid not only of inertia forces and inertia moments, but also from inertia and combustion torques.
It is not about a slight or substantial reduction of the “torque flactuation”, it is about the elimination of the “torque fluctuation”.
Did I mention any CFD?
Any time-area analysis?
Any Laser interferometry mapping?
No.
It is just the application of the basic physical laws, of geometry and maths etc.
Quote from Kelvin Cameron / CycleWorld link of J.A.W. regarding the unbelievable evolution of the 2-strokes through the years:
“What were their methods? CFD? Time-area analysis? Laser interferometry mapping? No, they did what we all did in those days; they tried stuff.”
If you take under account the “substantially longer piston dwell” characteristic of the OPRE engine and the rest advantages from its strange architecture . . .
(more at http://www.pattakon.com/pattakonOPRE.htm and http://www.pattakon.com/pattakonPatOP.htm and http://www.pattakon.com/pattakonPatPortLess.htm )
Thanks
Manolis Pattakos