http://scarbsf1.com/silv_test0204/BAR_serrated.htm
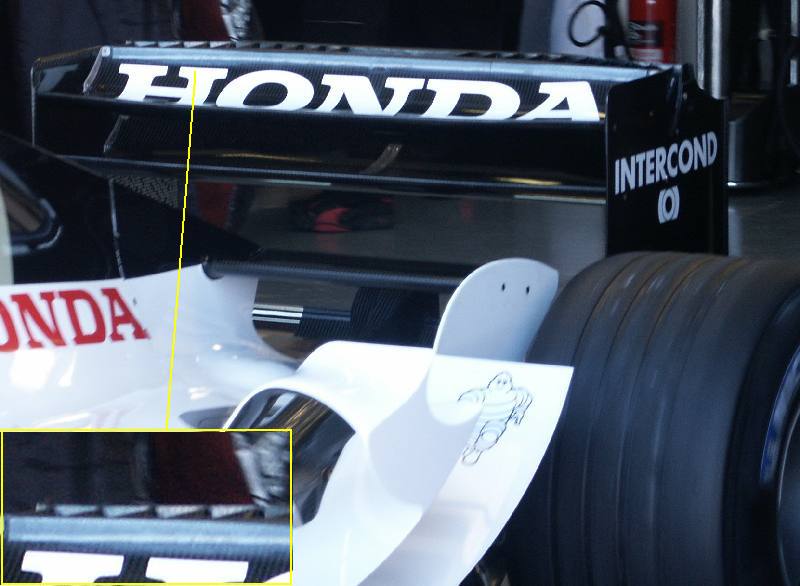
The point in the main element + flap design is to have two elements with a gap between them.marcush. wrote: so if this design serves to reduce the count of wing elements,why not bend over a Wingelement to form an extreme S-Shape and have the fold over end serve as a flap? Voila,one Element ,still a Flap function.
In all the longitudinal sections including the duct it would count as two elements.marcush. wrote: Another one just for the record:Why not put ducts into the Single element to actually form an interrupted slot ?
Are you referring to the control of boundary layer via suction or blowing (active high lift systems requiring holes on the surface of the wing) ?joseff wrote: I remember an article from way, way, in the last century (1980's or so, no kidding) about cross-drilling wings to lower their stall speed