Quite relative to the cracked cylinders and the thermal issues in aviation engines, are the issues (cracks, melting, overheating, scuffing, wear of cooperating parts) in the bridge of the exhaust port in several 2-stroke engines (water cooled or air cooled).
QUOTE from the page 136, post #2027 in this thread:
UtahTrailRide:
"Can someone explain to me what the deal is with drilling pistons on the exhaust side. I've heard the CR125 needs the piston drilled but I sure didn't in my last rebuild. Now I'm all paranoid I'm gonna shred something on the hot side."
ChrisLPD:
"OK, this is an old-school 2-stroke engine builder trick Utah,...but that one that works VERY Well! The idea is that the exhaust port bridge in the 2-stroke is a necessary evil. It is the one fault of the efficiency of a tuned 2-stroke engine. Its necessary because it acts as a land for the rings to run against as the slipper piston passes the exhaust port on its stroke to keep the ring compressed. It’s the evil because it’s the absolute hottest part of the motor and the absolute MOST suseptable to cylinder failure or nikasil plating damage for 3 reasons…
1. It is the thinnest section in the combustion chamber and can not dissipate heat. (Imagine taking a torch and heating the entire surface of a sewing needle. If you heat the needle’s eye, the shaft, and the point evenly, which part glows red first? The needle point does because it is the thinnest surface area that can not dissipate the heat).
2. All of the expanding burning hot gasses must pass by it. (Physics of Convection Dynamics)... (Imagine taking that same blow torch and blowing the flame evenly thru the center of your cylinder. It heats up in 360 degree radiation of the heat source. Now focus the flame onto one part of the cylinder. In addition to the heat from thermal radiance, the surface contact point heats up dramatically hotter because of the convection (movement) of the hot expanding gas molecules are bombarding and moving around it. Same thermal convection effect as the hot expanding combustion chamber gasses bombarding and having to move around the exhaust bridge.)
3. In lieu of both of the above critical faults, the exhaust bridge is NOT encompassed by the water jacket to get cooled
Most cylinder failures in a properly jetted and sealed 2-stroke with good fuel and lubrication are on the exhaust bridge because it gets so damned friekin hot. This is especially true of plated cylinders where you first start to see the plating flake off around the exhaust bridge. Drilling the the piston is MASSIVE insurance against this failure from the bridge warping, cracking, or flaking its plated coating. This was done by numerous factory teams and engine builders in the good'ole days before MX had cams, valves, and timing chains. This was when the manufacturers wanted to sale thumpers and pressured the AMA to establish the rules that a thumper was allowed twice the displacement to be "Fair" against the oil burners.
This is how its done...When I set up a 2-stroke, I use set-up dye. An easily removable (wipe-off) acrylic-like paint that you can spray on a part to visually inspect the wear and contact areas during motor building. I spray the dye on the front of the piston (exhaust side) and allow it to dry. I then install the piston on the wrist pin (without the rings) and lightly seat the cylinder down on it.
Once I have the cylinder lined up and seated, I look thru the exhaust port (open exhaust port with no pipe), I cycle the crank (via kick starter) until the bottom ring land passes approx ½ inch above the top of the exhaust port into the compression/combustion chamber. Using an etching tool I lightly trace both the outer left and right sides of the exhaust bridge into the set-up dye on the piston, and then disassemble.
Now with the piston removed I can see where the exhaust port bridge is in the etchings of the dye and I find the center vertical axis between these two etchings. This is the center of the exhaust port bridge. Starting ¾ of an inch below the ring land, I drill two .050 holes vertically (one on top of the other) about ½ inch apart down the center axis between the two vertical left and right marks.
The idea concept is to allow the positive pressure in the crank case (on the pistons downward stroke) to mist just a fine little amount of the cool, raw fuel/air mix onto the exhaust bridge thru the piston holes each time the piston passes the bridge. The cool, raw fuel mix acts as a cooling agent and will surprise you by how much this little trick will drop the temp of the thin little exhaust port. At 6000 RPM’s the critical heat temp on that thin little exhaust bridge is getting misted and cooled with fuel and intake air 100x a second!
Some will say this looses horsepower, I don’t believe so as long as you line the holes correctly and mist the center axis of the bridge and not vent your positive crankcase pressure out of the open exhaust port. Even if does, the loss is very, very, very minimal…but IT WILL SAVE YOUR $400 plated cylinder.
As frdbtr pointed out… This is a commonality of Wiseco recomendation in SOME of their piston kits that most people don’t read. (Some applications do not use a single port exhaust bridge). I am not familiar with the other Wossner brand he named, but wiseco recommends it because IT DOES WORK and their pistons are FORGED instead of cast and do not lose integrity by drilling the holes in the piston wall.
A Note about OEM and cast pistons… The same cooling effect would be benefited from an OEM or any other piston. It’s not often recommended for cast pistons because the “sand-cast” piston will weaken at the metallurgical level when you drill holes in it unless you stress relieve and re-harden it.
Please, please, consider all of the above My Opinion Only,... but as an educated opinion I have been building cast-iron and nikasil 2-stroke motors for 25 years and I have yet to have a cylinder failure of the exhaust bridge since I learned this from World Champion Melvin Cooper (Cooper Company Machine and Racing) building 2-stroke Hydroplane racing engines back in my twenties."
END OF QUOTE
QUOTE from http://www.millennium-tech.net/pistonTrouble.php

EXHAUST BRIDGE SEIZURE
Piston seizures can occur at the center exhaust-bridge on a delta-shaped port, or the sub-exhaust bridges on a triple port design. The exhaust bridge is the hottest are of a 2-stroke cylinder and the ring pressure is at its peak because the bridge’s surface area is so small. Seizures happen for many reasons but the most common are 1) Lack of lubrication 2) Too lean jetting or air leak 3) Coolant over-heating 4) Not enough bridge relief 5) No oiling holes in the piston over-lapping the exhaust bridge.
END OF QUOTE
In the PatATE each bridge has not just two tiny holes to cool down it; it has all the fresh cool air / mixture to pass around the bridges to cool down them.
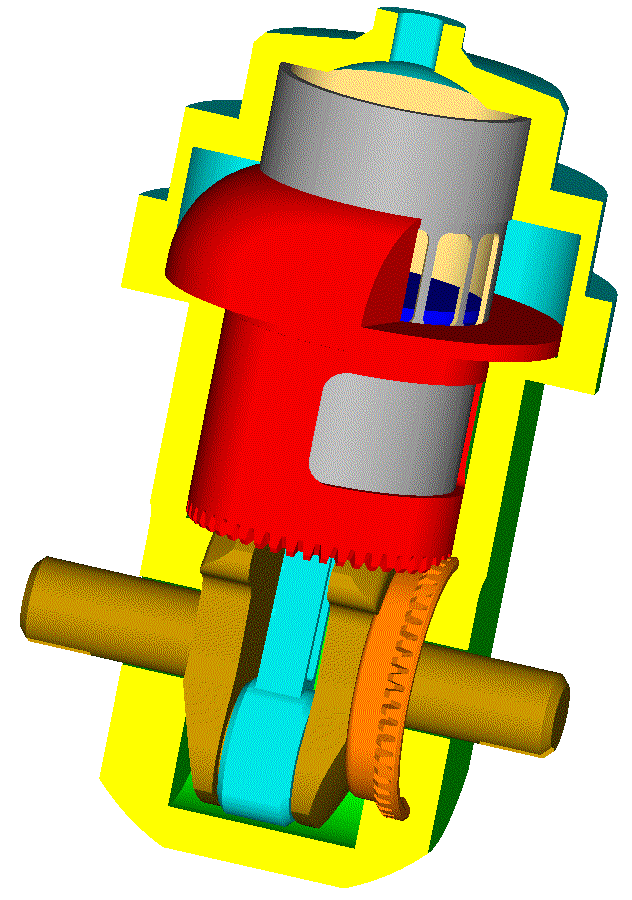
Reasonably, the temperature of the bridges of the PatATE can be about half of the temperature of a conventional 2-stroke exhaust port bridge.
END OF QUOTE
The substantial reduction of the peak temperatures in the 2-stroke engine means a lot in terms of reliability, of lube specific consumption, of clean exhaust, of TBO etc.
Combined with the asymmetric exhaust, with the asymmetric transfer:
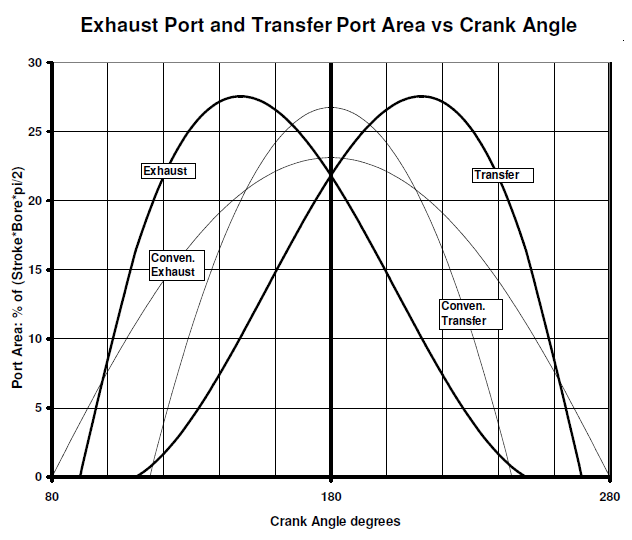
and with the asymmetric intake (without reed valves or conventional rotary or drum valves):
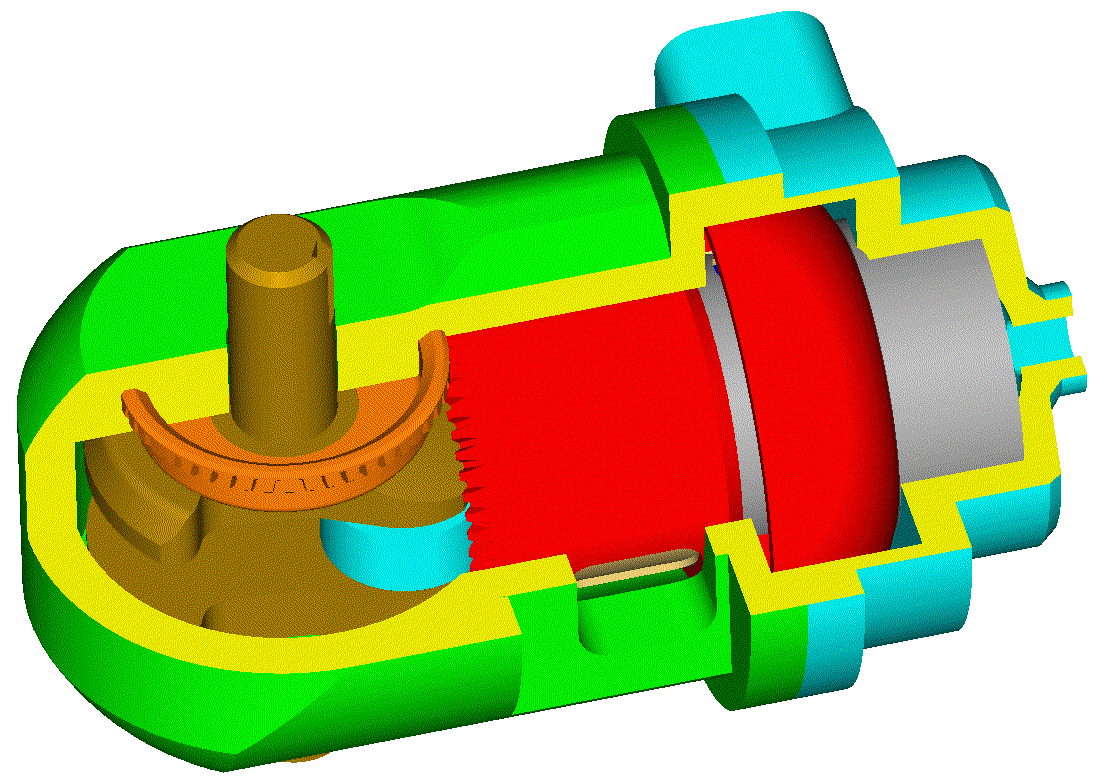
the PatATE 2-stroke seems a serious competitor for the 4-stroke engines.
Thanks
Manolis Pattakos