You write:
“btw these (including the one from a Master's) contain at least 3 faults .....
they wrongly state that the inline 4 .....
inertia torque reaches the road .... and wrongly ....
one of its cylinder's inertia torque is shown as different to the other 3 .... and wrongly ....
are in denial over the crossplane 4's invention in Germany 50+ years ago (it then won 2 world championships)”
Here are the correct plots of the free inertia force, torque and moment of the Cross-Plane-Crankshaft Uneven-Firing Straight-Four of Yamaha-R1 (with a first order balance shaft) and of the Flat-Crankshaft Even-Firing Straight-Four (the typical car engine):
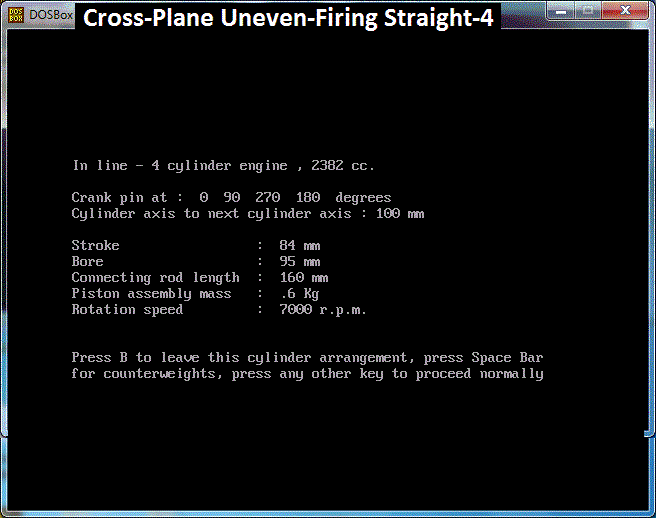
On the left axis you see what the plot is about; spot on the units per horizontal line.
The free inertia torque of the “Cross” is several times lower than what is presented in the plot:

of the https://mecaniblog.wordpress.com/2016/0 ... -approach/ article
In the plot:

of the same article the uneven firing of the “Cross” causes a significant asymmetry of the total (inertia and combustion) torque on its crankshaft: the expansion of the third cylinder continues after the ignition / start of expansion of the fourth cylinder, while after the end of the expansion of the first cylinder it is a period during which there is no combustion / expansion).
Is this the plot you mean by “one of its cylinder's inertia torque is shown as different to the other 3”?
You also write:
“regarding engine inertia torque pulses ..... attenuation by frequency separation isn't attenuation by damping .... isolation from either combustion or inertia pulses involves only tiny losses
some isolation is inherently and unavoidably present eg in the compliance of a transmission's shafts etc”
The idea behind the Yamaha-R1 project (as the Suzuki engineers – not the journalists - explain) is to compete / win the conventional arrangements by providing better feeling of the rear tire hooking to the driver.
Its uneven firing is a problem for the peak power.
Its inherent loads require stronger / heavier casing.
Its strong inertia-moment requires the addition of a 1st order balance shaft (more friction, more weight).
Despite all these, Yamaha was the permanent winner in moto-GP for several years. I.e. the idea of eliminating the inertia torque passing to the transmission / rear tire did work.
On the other hand:
The uneven firing is not accepted in car engines: the driver / passengers will feel as something is wrong with the engine.
If, using dampers, the second order inertia torque of the Even-Firing Flat-Crank Straight-Four is isolated, a part of the combustion torque is also isolated / consumed (the rest moto-GP teams / makers knew about dampers, isolation etc, etc, however they failed to win Yamaha’s R1).
And with the strong inertia torque of the Flat-Crank Straight-Four passing to the transmission, the friction in the transmission is increased, as well as the noise and the vibrations.
You also write:
“I have never said anything against the PatVRA as enabling what we might loosely call 'the poor man's crossplane'
As explained in the previous, the “crossplane” comes together with issues / side-effects.
The PatVRA does what the “crossplane” without having the issues / side-effects of the “crossplane”.
If you can have:
- the even-firing of the Flat Crank
and
the better-feeling (of the rear tire hooking) of the “crossplane”
and
the lower weight and cost of the Flat Crank,
and
the higher power of the Flat Crank,
The one is a compromise, the other is a solution
So, what makes the PatVRA 'the poor man's crossplane' ?
Thanks
Manolis Pattakos